I took a machine shop class at the College of Du Page this fall, I also took a machine shop class over the summer. Tonight was the last night of the class, and I was finishing my last project, which was a
filing jig. I already have one I bought, so I made mine a little different, I gave it a 30 degree angle instead of a 45 degree angle. The tool suppliers say they are good for holding pieces to saw. I think they are terrible for sawing, I just like them for filing, mostly I just use them for 90 degree angles. I don't use it very often, but when I need it I think its great. Like for filing all those rivet spacers on my teapot.
I only took a couple pictures of making it. This is a horizontal mill, I am cutting the grooves to hold wire or tubing. I am using that large cutter to cut the tiny grooves cause it was the only one that had the angle I wanted. Its 120 degrees, the smaller cutters were around 90 degrees or less.

I am cutting the grooves on the middle piece of the tool. The side opposite the one I am cutting has the 30 degree angle, so I needed something to hold it at 90 degrees while I cut the flat side. That's why its in a smaller vise in the bigger vise.

Mine is the one on the bottom. I still need to drill holes in it, harden and temper it, and grind it. The one I bought is on the top. Mine is made of 1/2" thick O-1 steel, the one I bought is about 1/4", or maybe a little thicker.

This is after the holes have been drilled and it has been heat treated.


This I after I made the rods to hold it together. The rods are 1/4" O-1 steel. At this step all that's left to do is grind it with the surface grinder and make some nuts to hold it together. I have been using normal nuts from a hardware store till I can make some nicer ones.

Grinding is done. But there was a problem. After it was made nice and smooth and shiny from grinding I was able to see fine cracks all over. The most are on the top piece, the middle piece has a bunch, and there's a few on the bottom piece. I showed it to my two instructors, they didn't know why it happened. One of them was there when I did the heat treating, after hardening it, it wasn't more than maybe 5 minutes before it went in the oven for tempering. We looked at them under a microscope, they don't look deep, so I think it will be
ok. But I really don't like these cracks. They said maybe I could grind them out... but since we don't really know how deep they are maybe I would end up grinding all night. I didn't feel like grinding it more.


Here are some photos of the cracks.


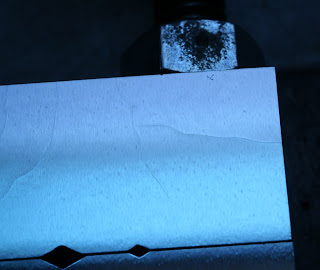